The world of footwear is undergoing a radical transformation, driven by the revolutionary power of additive manufacturing. Forget mass-produced, one-size-fits-all shoes; the future is here, and it’s all about 3D printed sneakers. This innovative approach is not just a passing trend; it's a paradigm shift, promising unprecedented levels of customization, performance, and sustainability, fundamentally changing how we design, produce, and even wear our shoes.
From elite athletes seeking marginal gains to fashion enthusiasts craving unique statements, 3D printing offers a solution that traditional manufacturing simply cannot match. Imagine a shoe perfectly molded to the contours of your foot, engineered for your specific gait, and designed with an aesthetic that is uniquely yours. This isn't science fiction; it's the tangible reality that 3D printed sneakers are bringing to life, opening up a world where footwear is no longer just an accessory, but an extension of the individual.
Table of Contents
- The Dawn of a New Era in Footwear: 3D Printed Sneakers
- Why 3D Printed Sneakers? Unpacking the Benefits
- The Art and Science of Designing 3D Printed Sneakers
- The Printing Process: Bringing Designs to Life
- Overcoming Challenges in 3D Sneaker Production
- The Future is Now: Innovations and Market Impact
- Where to Find Inspiration and Models for 3D Printing
- Getting Started with Your Own 3D Printing Journey
The Dawn of a New Era in Footwear: 3D Printed Sneakers
For decades, sneaker manufacturing has largely relied on conventional methods: cutting, stitching, and gluing various components together. While effective, this process has inherent limitations in terms of design complexity, material waste, and the ability to truly customize products for individual users. Enter 3D printing, also known as additive manufacturing. This technology builds objects layer by layer from a digital design, allowing for intricate geometries and functional structures that were previously impossible to achieve. When applied to footwear, this means creating midsoles with complex lattice structures that offer tailored cushioning, or uppers that are breathable in specific zones and supportive in others, all from a single, continuous process.
Major players in the sportswear industry, such as Adidas with its Futurecraft 4D series and Nike with its Flyprint technology, have already invested heavily in this space, showcasing the immense potential of 3D printed sneakers. These early adopters are not just demonstrating a new way to make shoes; they are redefining what a shoe can be. The ability to prototype rapidly, iterate designs quickly, and eventually produce on-demand opens up entirely new business models and consumer experiences. This shift is not merely about novelty; it's about efficiency, performance, and a future where footwear is as unique as the person wearing it.
Why 3D Printed Sneakers? Unpacking the Benefits
The allure of 3D printed sneakers extends far beyond their futuristic appearance. The technology offers a compelling suite of advantages that address some of the most pressing challenges in the traditional footwear industry, from environmental impact to consumer demand for personalized products.
Unparalleled Customization and Personalization
One of the most significant benefits of 3D printing is its capacity for personalization. Imagine a running shoe where the cushioning and support are precisely calibrated to your weight, gait, and foot strike pattern. Or a fashion sneaker that reflects your unique style with intricate, bespoke patterns and textures. Traditional manufacturing struggles with this level of individualization due to the high costs and complexities of tooling and production lines for small batches.
With 3D printing, each pair of 3D printed sneakers can be a unique creation. Designers can create custom parts and unique designs that are impossible with conventional methods. This means moving beyond standard shoe sizes to a truly bespoke fit, improving comfort, reducing injury risk for athletes, and offering unparalleled aesthetic freedom. The dream of having a shoe that is truly "yours" becomes a tangible reality, allowing for interactive and configurable designs that adapt to individual needs and preferences.
Sustainability and Reduced Waste
The traditional footwear industry is notoriously resource-intensive and generates significant waste. Cutting patterns from sheets of material inevitably leads to scrap, and the multi-component assembly process often involves adhesives and solvents with environmental impacts. 3D printing, by its very nature, is an additive process, meaning it only uses the material necessary to build the object, leading to significantly less material waste. This is a crucial advantage in an era where environmental consciousness is paramount.
Furthermore, the ability to print on-demand reduces the need for large inventories and minimizes overproduction, a major contributor to waste in the fashion industry. Companies can produce only what is sold, leading to a more efficient and sustainable supply chain. The potential to use recycled or bio-based filaments for 3D printed sneakers further enhances their eco-friendly credentials, paving the way for a truly circular economy in footwear production.
The Art and Science of Designing 3D Printed Sneakers
The creation of 3D printed sneakers begins long before any material is laid down by a printer. It starts in the digital realm, where designers blend artistic vision with engineering precision. This phase is critical, as the quality and functionality of the final product are entirely dependent on the digital model.
From Concept to Digital Model: Essential Tools
Designing 3D printed sneakers requires specialized software that allows for the creation and manipulation of three-dimensional objects. These 3D design software options make it possible for designers to create and refine 3D CAD designs easily. For beginners and hobbyists, tools like Tinkercad offer a free web app for 3D design, electronics, and coding, providing an ideal introduction to the world of digital fabrication. Similarly, SketchUp Free is lauded as the simplest free 3D modeling software on the web, with no strings attached, allowing users to bring their 3D designs online and access their projects anywhere.
More advanced users, including 3D artists and game developers, might turn to tools like Figuro, a free online 3D modeling tool that enables quick and easy creation of 3D models. For professional-grade work, comprehensive software suites like Autodesk's 3D design software options are global leaders in design and make technology, offering powerful tools for modeling, animation, textures, and more. Blender, another robust and free open-source tool, provides a comprehensive array of modeling tools that make creating, transforming, and editing your models a breeze. These platforms allow designers to create 3D objects, edit materials, add interactivity, and ultimately control the outcome of their 3D design work, transforming abstract ideas into tangible designs.
Interactive Design and AR/VR Integration
The design process for 3D printed sneakers is increasingly becoming interactive and configurable. Designers can now visualize and manipulate their creations in real-time, making adjustments on the fly. This level of interactivity is further enhanced by the integration of Virtual Reality (VR) and Augmented Reality (AR) technologies. Imagine stepping into a VR environment where you can virtually "try on" a 3D printed sneaker design, rotating it, inspecting its details, and even simulating how it feels on your foot.
AR applications allow designers to overlay digital models onto the real world, enabling them to see how a new sneaker design would look in a physical space or on a person's foot before it's even printed. This capability works with all operating systems, browsers, and devices, making it accessible to a wide range of creators. Such immersive design experiences accelerate the iteration process, reduce the need for physical prototypes, and ensure that the final 3D printed sneakers meet both aesthetic and functional requirements with unparalleled precision.
The Printing Process: Bringing Designs to Life
Once a digital model of the 3D printed sneakers is finalized, it's sent to a 3D printer. There are several types of 3D printing technologies suitable for footwear, each with its own advantages:
- Fused Deposition Modeling (FDM): This is the most common and accessible type, where a thermoplastic filament is melted and extruded layer by layer. It's great for prototyping and less complex structures.
- Stereolithography (SLA) & Digital Light Processing (DLP): These technologies use a liquid resin that is cured by a UV laser or projector. They produce highly detailed and smooth objects, ideal for intricate midsoles and fine details.
- Selective Laser Sintering (SLS): This method uses a laser to fuse powdered material (like nylon) layer by layer. SLS is particularly well-suited for footwear due to its ability to create flexible, durable, and complex lattice structures without the need for support material, making it perfect for midsoles that offer specific cushioning and energy return.
The choice of technology depends on the specific requirements of the 3D printed sneakers, including desired material properties, resolution, and production volume. For instance, high-performance athletic shoes might utilize SLS for their midsoles due to its material versatility and structural capabilities, while fashion-focused sneakers might leverage SLA for intricate aesthetic elements. The process ensures that from product models to printable parts, 3D design is the first step in making big ideas real, ultimately delivering a product with unprecedented precision and functionality.
Overcoming Challenges in 3D Sneaker Production
While the potential of 3D printed sneakers is immense, there are still challenges to overcome before they become a mainstream commodity. One significant hurdle is the cost of materials and industrial-grade 3D printers. While consumer-level printers are becoming more affordable, the specialized materials and high-precision machines required for durable, performance-oriented footwear can be expensive, impacting the final price of the shoes.
Another challenge lies in material science. Developing filaments and resins that possess the ideal combination of flexibility, durability, breathability, and comfort for footwear is an ongoing area of research. Traditional shoes use a variety of materials for different components (e.g., rubber for outsoles, foam for midsoles, fabric for uppers), and replicating this multi-material functionality with a single 3D printing process or a limited range of printable materials is complex. Furthermore, the speed of printing for large-scale production still needs improvement to compete with the rapid output of conventional factories. However, continuous advancements in both printer technology and material development are steadily addressing these issues, pushing 3D printed sneakers closer to widespread adoption.
The Future is Now: Innovations and Market Impact
The future of 3D printed sneakers is not a distant dream; it's unfolding before our eyes. We are witnessing rapid innovations in materials, printing speeds, and design software that are making these shoes more accessible, affordable, and functional. Companies are exploring hybrid models, combining 3D printed components with traditionally manufactured parts to leverage the best of both worlds. Imagine a shoe with a 3D printed midsole tailored for your foot, combined with a conventionally manufactured upper for comfort and style.
The market impact is profound. It promises to democratize design, allowing smaller brands and individual designers to compete with established giants by offering highly customized and unique products. It also shifts the focus from mass production to personalized, on-demand manufacturing, potentially reducing waste and fostering more sustainable practices across the industry. The integration of "probably the best tracker in the market" into 3D printed footwear could provide real-time performance data, further enhancing personalization and training insights. The ability to create interactive and configurable products that are VR and AR ready means consumers will be able to engage with their footwear like never before, fostering a deeper connection with their purchases.
Where to Find Inspiration and Models for 3D Printing
For anyone looking to delve into the world of 3D printed sneakers, whether for inspiration, learning, or finding printable files, the internet offers a vast treasure trove of resources. The collaborative nature of the 3D printing community means there's an abundance of shared knowledge and designs.
Exploring Digital Marketplaces and Communities
Digital marketplaces and model libraries are invaluable resources. Thingiverse, for example, is a go-to place where you can find custom parts to unique designs and discover and download the best 3D models for all your projects. It's part of the world’s largest 3D model library, where you can share your models and get inspired. Similarly, TF3DM (The Free 3D Models) hosts over 15,000 3D models in various formats, making it the go-to place where you can share your free 3D assets and download instantly any you like.
Cults is another prominent digital marketplace for 3D printing and design. You can use their 3D model library to discover everything you can do with a 3D printer (FDM, SLA, DLP, SLS) and even with CNC machining. These platforms, often with a community of over one million creators, are the world’s largest to publish, share, and discover 3D content on web, mobile, AR, and VR. They embody the spirit that "if you can dream it, you can build it," making it easier than ever to find inspiration, learn from others, and even download millions of 3D models and files for your 3D printer, laser cutter, or CNC machine, paving the way for your own 3D printed sneakers.
Getting Started with Your Own 3D Printing Journey
The prospect of designing or even printing your own 3D printed sneakers might seem daunting, but with the right resources and a willingness to learn, it's more accessible than ever. Start by exploring the free 3D modeling software mentioned earlier, such as Tinkercad or SketchUp Free, to get a feel for 3D design. There are countless tutorials available online that can guide you through the basics of creating 3D objects, editing materials, and understanding how to prepare a model for printing.
Once you're comfortable with design, consider investing in a beginner-friendly FDM 3D printer, which offers a great entry point into the world of additive manufacturing. Experiment with different filaments and settings to understand how they affect the final print. Remember, 3D design has never been easier, and from product models to printable parts, it's the first step in making big ideas real. The journey of creating 3D printed sneakers is a blend of creativity, technology, and continuous learning, promising a rewarding experience for anyone who dares to step into this exciting future.
Conclusion
The emergence of 3D printed sneakers marks a pivotal moment in the footwear industry, signaling a shift towards hyper-personalization, sustainability, and innovative design. From the intricate lattice structures of midsoles to custom-fit uppers, 3D printing offers a level of precision and customization previously unimaginable. While challenges remain in material science and production scale, the rapid advancements in technology and the burgeoning community of designers and enthusiasts are quickly overcoming these hurdles.
The future of footwear is undeniably 3D, promising not just shoes, but truly bespoke experiences tailored to every individual. We encourage you to explore the fascinating world of 3D design and printing. Have you ever considered designing your own footwear? Share your thoughts and ideas in the comments below, or better yet, share this article with friends who might be interested in stepping into the future with 3D printed sneakers!
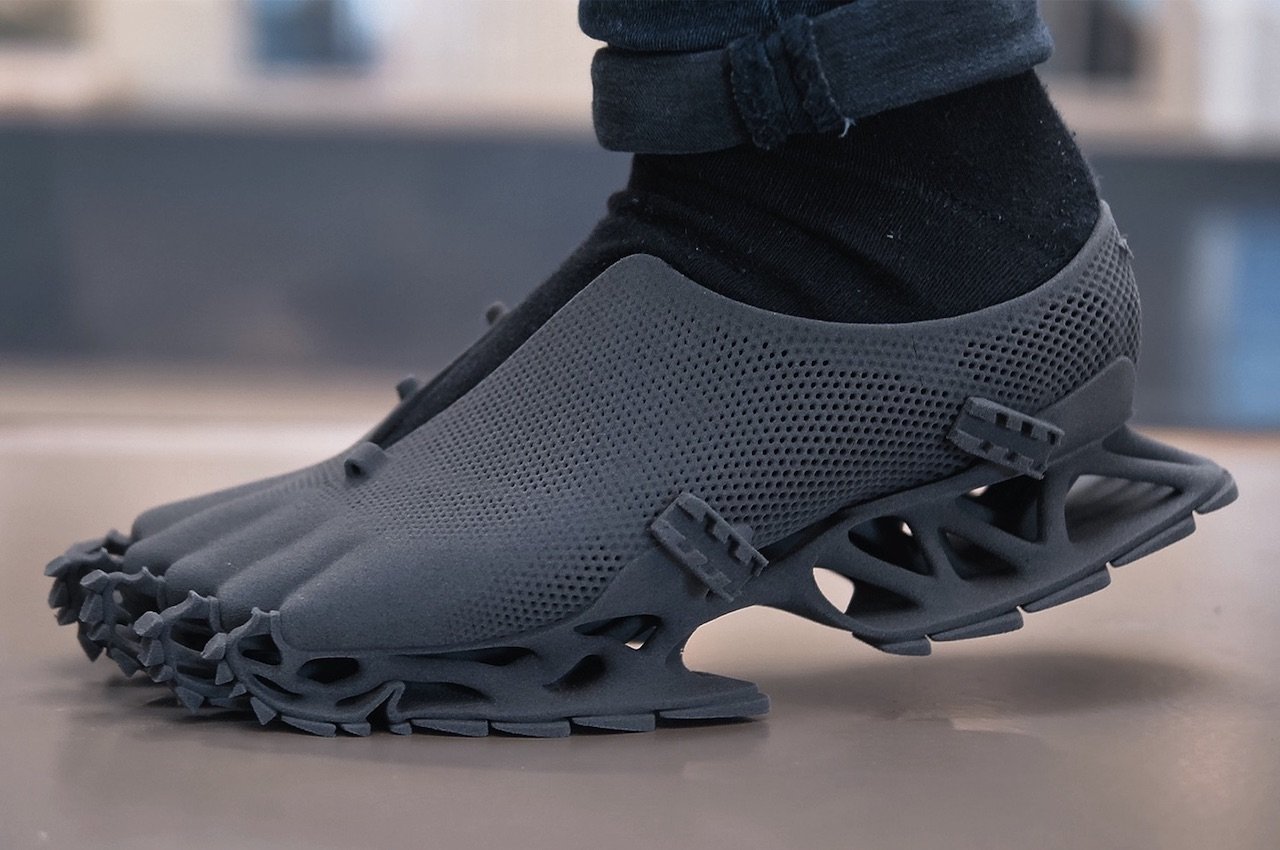
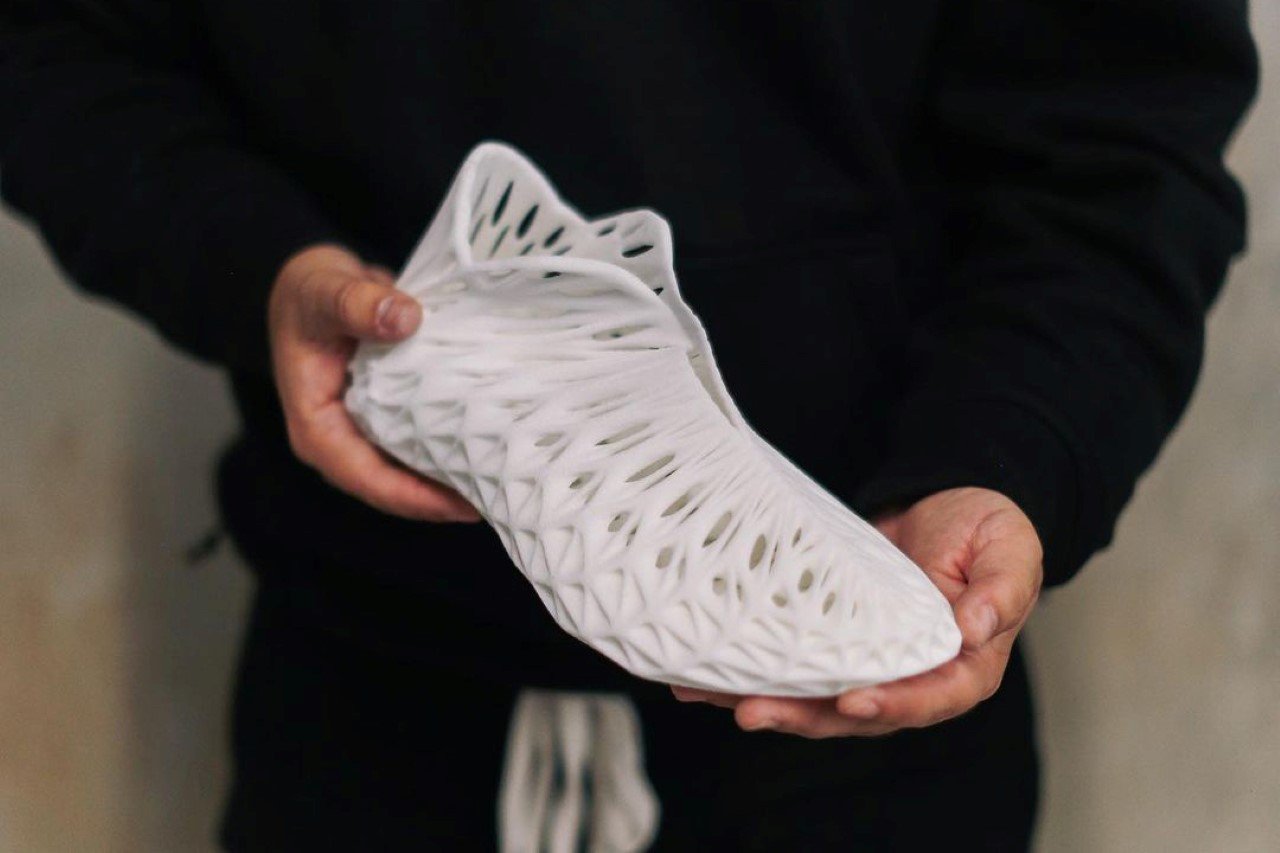
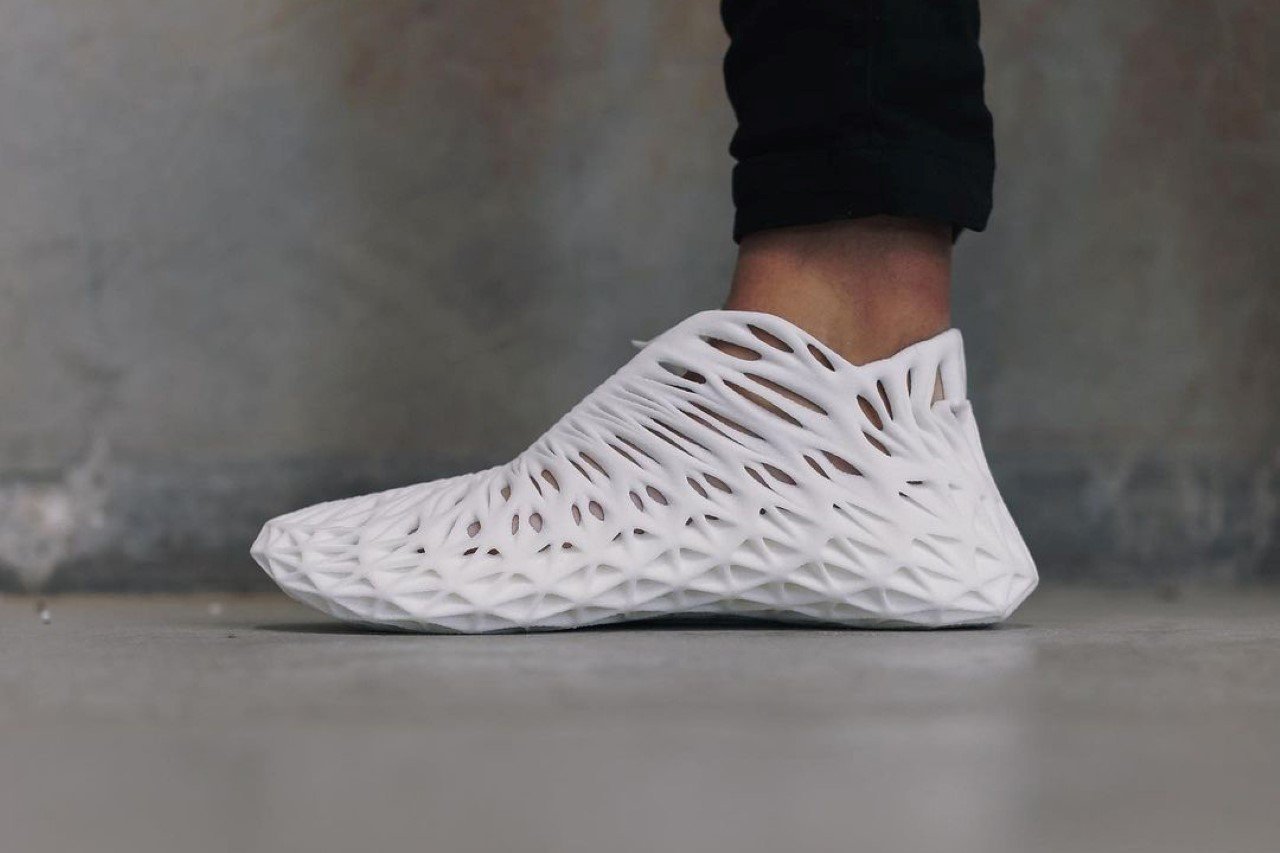
Detail Author:
- Name : Dixie Rohan
- Username : matilda31
- Email : lynn77@hotmail.com
- Birthdate : 1972-10-27
- Address : 5326 Clay Terrace Apt. 004 South Heloise, OK 98780
- Phone : +13208880036
- Company : Morar, Hudson and Bins
- Job : Welding Machine Operator
- Bio : Repellat nisi quam earum quasi cum. Perferendis quia deserunt in aliquam. Nesciunt ea rerum sint enim velit harum.
Socials
facebook:
- url : https://facebook.com/avon
- username : avon
- bio : Quibusdam quos error vitae dolorum a non rem.
- followers : 5166
- following : 2493
twitter:
- url : https://twitter.com/vona
- username : vona
- bio : Accusantium dolore alias sit dolorem. Sit dolores odit molestiae qui reiciendis nesciunt ea.
- followers : 5966
- following : 1766